Early in the year 2016, my wife Lynne and I took collection of a shipping crate containing a Moffat Virtue MV3 engine and pump which my good friend in Australia, Ken Cummings, had sent to me as a 70th birthday present. This engine, Serial Number 31172, is rated at 2¼hp @ 1,000rpm and dates from the 1940s.
Once home, the first task was to remove the said items from the crate, which took some time as this was exceedingly well constructed, and then take some photos. Having already restored one Moffat Virtue MV3, it made me realise how small the engine is without the trolley and tanks (petrol and water).
Due to all the trauma of selling my business, which then required moving ten years of treasures and club items from my workshop to home, the engine’s restoration was put on the back burner for a while.
When work started on the engine, the first job was to spray all nuts and bolts with WD40 and repeat this several times over a period until we had a suitable space in the workshop to allow the engine to be worked on.
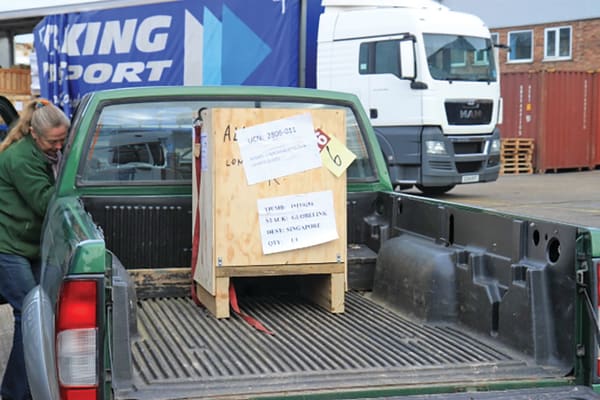
I soon realised, that had the engine not been gifted to me and travelled half way round the world, I think I would have given up in the early stages of restoration. If it had been a Lister D Type engine, the most popular engine here in the UK, I think I would have sold it as parts. However, due to the generosity of Ken Cummings I felt that I had to carry on, but as it became impossible to do much of the work myself, what with everything else happening in my life at the time, I called on a good friend, Lawrie, for moral support. In fact, Lawrie ended up doing nearly all the work, for which I am most grateful.
Major problems
The first major problem arose when a number of the studs broke whilst removing the cylinder head, leaving just two to come undone without any trouble. This meant drilling and tapping fresh holes. It was discovered that the exhaust valve was stuck, so it was sprayed with releasing fluid and left to soak for a couple of days. When it was finally removed it was found that the stem was badly wasted and needed replacing. It was sent as a pattern to Cox & Turner, regular advertisers in the Classified advertising pages of Stationary Engine Magazine. The rings were stuck in their grooves so they were left to soak for a few days in Coke (the soft drink) after which they could be removed, at which time they were deemed not suitable for re-use, so new rings were ordered along with the new exhaust valve.
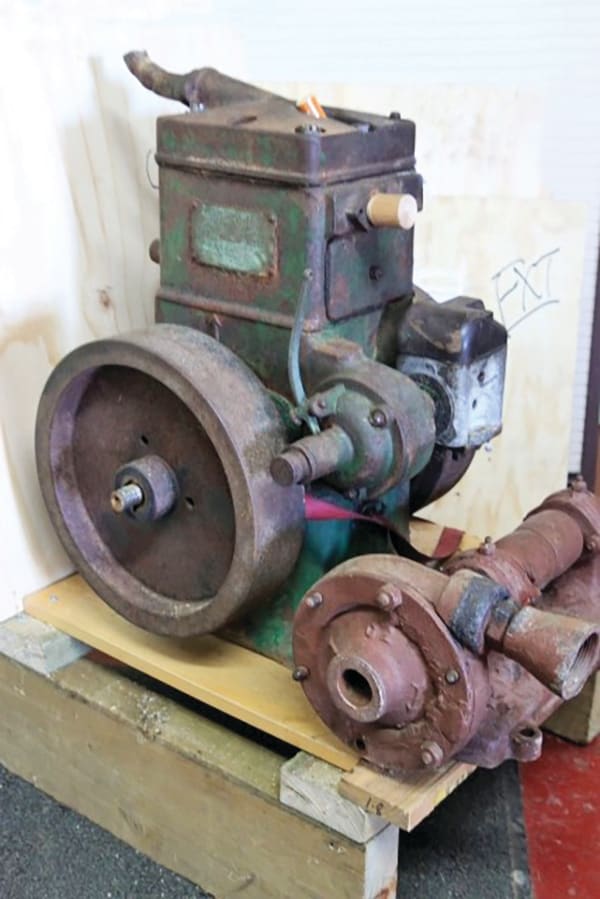
The next job involved the removal of the cover plate to get to the big-end; here, we were greeted by about an inch of sludge in the bottom, and the rest of the sump full of water. I think the engine must have been stored in wet conditions as not only was there water in the crankcase but the lower half of the engine and flywheels were very rusty and pitted.
Upon removing the con-rod it was found that the bearings were in good condition, but with plenty of movement (there were plenty of shims to remove to take out the slack) so that was OK.
While waiting for the delivery of parts from Cox & Turner, there was time to clean out the water jacket of debris, rust, and lime-scale; in fact there was enough to fill a small shovel. Most of the holes were drilled out except the two exhaust outlets as they curved around the casting. We managed to get enough of the lime-scale out to be able to use ‘Viakal’ scale remover. After a couple of days, the scale had softened enough to allow it to be removed using a thin metal rod.
Valve seats re-cut
At this point, the piston was cleaned, the valve seats re-cut and the valves ground in. We removed the crankshaft castings, with bearings, but only after having to use a heavy-duty puller to remove the flywheels; they are coned and were rusted on. It required 3½ tons on the gauge before they came free. The oil holes in the bearings were blocked and a little slack on the crank was discovered. After giving everything a good clean, the crankshaft was put back in position with new handmade gaskets. When it came to fitting the new oversize rings, we found that when gapped tight at the bottom of the cylinder, they were gapped 25 thou at the top.
New pattern head studs were fitted to replace those broken or missing. However, when the cylinder head, complete with a new copper gasket was fitted, four of the seven new studs pulled out of the block when the nuts were torqued down. This meant removing the head again and re-tapping the block to take oversize studs - all time consuming.
Moving on to the magneto; this was found to be in a ’bit of a state’ but after a strip down and a good clean, it delivered a faint spark. However, when checking the rotor timing it was found that the cam was in the wrong place; after re-timing there was a very strong spark.
All paint and rust was removed and the castings treated with an anti-rust treatment, followed by two coats of red oxide, then two of undercoat and finally two top coats.
Still more problems
It was time to put everything back together. The flywheels were fitted, as was the carburettor, and a makeshift exhaust. When the water tank was filled, it was discovered that the cylinder head was leaking. It appears that when the head nuts were tightened the other three studs had pulled out of the block; it was found that the metal was very poor quality.This meant more oversized bolts were required and all the work that that involved.
Come the day of the engine’s first start-up, after an hour of swinging the handle, it just refused to start. Everything was checked and double-checked; the timing marks matched, there was fuel in the carburettor, but still it was no-go. It was time to try some old tricks, so it was out with the pencil and the sparkplug electrode leaded. Amazing how some of the old tricks work, for after just a few swings on the starting handle the engine fired, and after a little fiddling with the fuel mixture, it was running but very fast. A stronger throttle spring was tried, which together with altering the governors considerably slowed the beat. After a run of about 30 minutes, I looked into the water tank only to see a trail of bubbles. A few choice words were uttered.
As the engine was hot, I pulled the head down a little more only for another stud to pull out. So it was off with the head yet again and the offending stud was replaced. When replacing the head, the old gasket, which was a little thinner than the new one was used; this seemed to solve the problem.
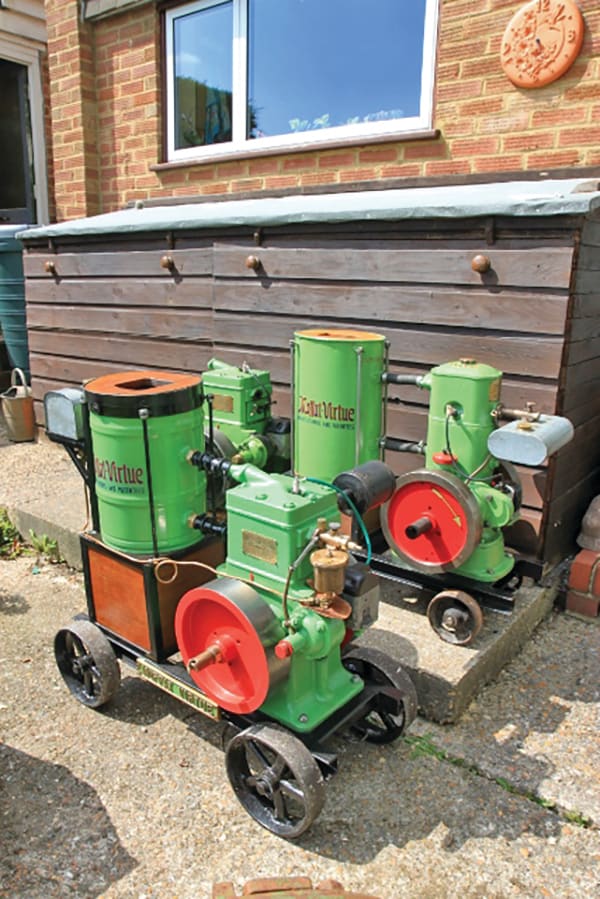
The next day, when the sparkplug was removed, it was found to be very oily, so with a new plug installed, the engine started after just three turns of the handle. It was run for four hours with the fuel mixture and air control being altered, but the engine still ran all over the place. The next thing to try was altering the timing; the line where the points start to open was 1½ inches from the Top Dead Centre (TDC) mark. The timing was reset at TDC and tried again. The engine now started better and ran a lot smoother.
After another four hour run, it was noticed that oil was leaking out of the crankshaft bearings, so it was off with the flywheels again. By now I was thinking to myself, where do I get new bearings for an Australian engine? Not wanting to strip everything down again, a set of felt seals were made and fitted between the flywheel boss and the bearing casting, also a tube was fitted over both castings with a small drain hole, which has stopped oil spraying on the side of the engine and up the side of the water tank.
Rally debut
After a year of scraping, de-rusting, freeing everything off, and calling it all the names under the sun except a Moffat Virtue (“The Muppet” was the politest), the engine was now running.
So we had the birthday present ready to rally, and it made its debut at the Amberley Museum & Heritage Centre ‘Spring Mechanicals Day’ on 30th April 2017, where it ran faultlessly. In case you think you have seen the engine before, we had to remove my other MV3 and use the existing trolley to save time.
There is still the pump to restore, but this hopefully will not take so much time...and I thought this was retirement!!!
I would like to say a big Thank You to Ken for gifting me the engine and pump, and to Lawrie for all the work he put in on its restoration.
*Alan Cullen (as narrated to Patrick Knight)