In the early 1900s, the growing Gippsland township of Warragul in Victoria realised a need for a more adequate supply of fresh water with existing supplies being of limited quality and quantity.
In 1906, engineer Mr Thomas Fowler was appointed to establish a fresh water supply, and he subsequently decided to erect a pumping station on the Tarago River, some 12kms from Warragul, at the small sawmilling township of Rokeby. The sawmills have now gone but the town lives on.
Pumping commenced in February 1910, using two Hornsby & Sons 37hp gas engines and a complete gas producing plant, driving Robison Bros 5-chamber 10,000gph centrifugal pumps, lifting the water with a 360ft head to a storage basin elevated above the township with a gravity run from there on, ultimately resulting in one of the highest pressures in rural water supplies of 120psi.
The Hornsby engines continued service through to 1923 when a 50hp Crompton DC electric motor was introduced and the No. 1 Hornsby was retired. As mains power had not reached the area in the 1920s, the Crompton 50hp DC motor was connected to an electrical supply from a water wheel generation system based some 28kms away on the Tooronga River at Noojee, which was supplied by the Latrobe Power Company. Very little information can be found on the generating plant or its life span with only basic foundations remaining today.
In January 1929, a contract was given to Ballarat manufacturers, Ronaldson & Tippett, to supply an engine of sufficient capacity to run the plant, resulting in the residual oil, direct injection engine, No. 7256, being produced. This was an air-start 68hp at 300rpm, 11¾ inch bore, 20 inch stroke, 7’9” flywheel unit, along with the 1926 Austral No. 7086 starting engine, coupled to a single-cylinder air compressor/generator/air receiver.
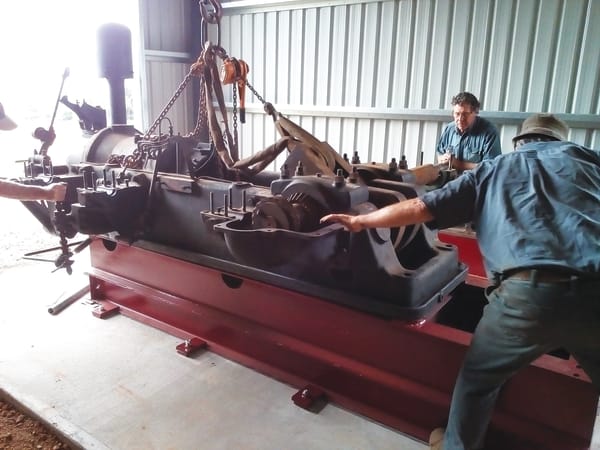
A branch rail line was constructed from the main Noojee line to the pumping station in order to bring the Ronaldson & Tippett to its destination.
The Ronaldson & Tippett appears to be of a Campbell design, although no identification has been cast into the base ( the only identification is on the brass ID plaque), coupled via a 6 inch flat belt driving through a 2-speed Richardson gearbox to a Kelly & Lewis triple-throw positive displacement pump, with a capacity of 15,000gph at 55rpm. It commenced operation in December 1929 until electrification in 1949/50. The Crompton and No. 2 Hornsby were taken from service when the Ronaldson & Tippett came on line.
It is believed Ronaldson & Tippett, Ballarat, only produced two engines of this size, with one going to West Australia to drive a power plant though its survival or existence now is unknown. The design appears identical to a Campbell, as seen at the Old Brook Pumping Station in the UK.
Fast forward to 1988...
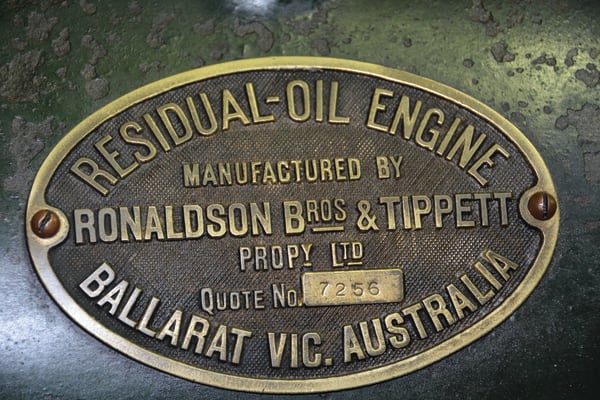
With a change to the Water Board and closure of the pump station, the engine club of the day were given the opportunity to remove all of the equipment from the site, which was a mammoth task as the site of the building was perched on the edge of the Tarago River in steep terrain. A dozer was needed to cut in a path to the site. The side of the building was removed and later reinstated to allow 4WD crane access. Removal of all components needed to be completed in a short time frame.
Congratulations go to those members, some of whom are current members of the Baw Baw Old Engine Club (BBOEC) as they were the saviours of all of the removed parts, which were then placed into private storage for the next 26 years.
A bureaucratic dispute over ownership continued for a number of years to finally be resolved in November 2014, with full ownership granted to BBOEC
With a truckload of components arriving at the BBOEC shed, the club developed a plan of attack on how to rebirth the Ronaldson & Tippett and the associated equipment. The first item on the agenda was to apply for a heritage grant in order to fund the project. A successful grant application allowed an extension to the club shed of 12m x 8m. Works commenced, beginning with foundations being formed. As the shed is on a landfill site, concerns were raised concerning stability of the ground, resulting in footings requiring 12m of concrete to a depth of 4’, with success.
A base was fabricated from I-beam and bolted down securely to the foundations. When reassembling the engine, a seized piston was discovered, the removal of which required many tonnes of pressure and a sledge hammer, before it was slowly extracted to reveal that water had entered during storage. Fortunately, the piston was at the top of the cylinder limiting the damage. A homemade hone fabricated from timber to a size of 11¾ inch was able to do the job nicely. New rings were manufactured and fitted, replacing the damaged and worn ones.
Next on the list was to fit the flywheel to the crankshaft - not an easy task with the crane driver estimating 3 ton in weight. On fitting the crankshaft back in place, it was found that the big end bearing was worn beyond repair. This was too much for the club workshop, and with the need for it to be remetalled, it was sent to a specialist in the field. On its return, hours of work were spent blueing, scraping, and bedding it back in.
Many other tasks included reseating valves, fitting a cooling tank, the sideshaft, governor, injection pump, lubricator, air lines, and exhaust system just to name a few.
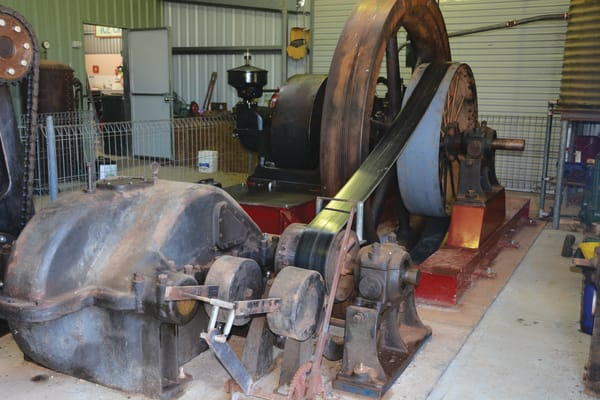
Finally, it was time for a test run. As the engine is air start, pressure was raised with no results. After a long time fruitlessly searching for the fault, frustration continued, leading to the abandonment of the air system in favour of a tractor and belt pulley. We finally achieved success, and for the first time in 30 years, the engine had sound and motion. There were smiles all around, knowing the engine was now in running order. The starting air system was seriously investigated, with the culprit found to be a badly worn injection valve. This was sent back to the lathe to be rebuilt, and once fitted, success reigned.
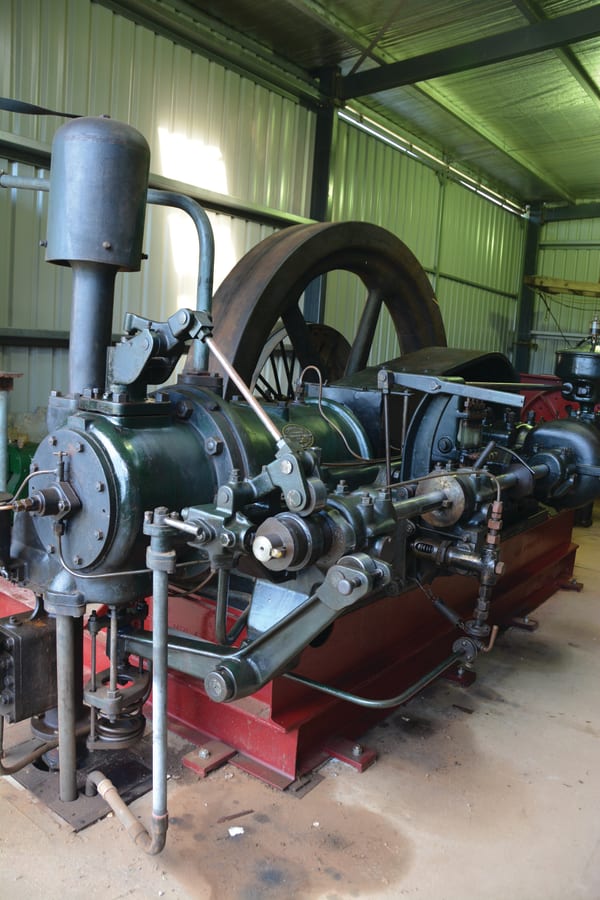
As the pump and gearbox were originally direct coupled due to floor level differences, we devised a chain drive system, which is the only new item we have had to fabricate for the entire project.
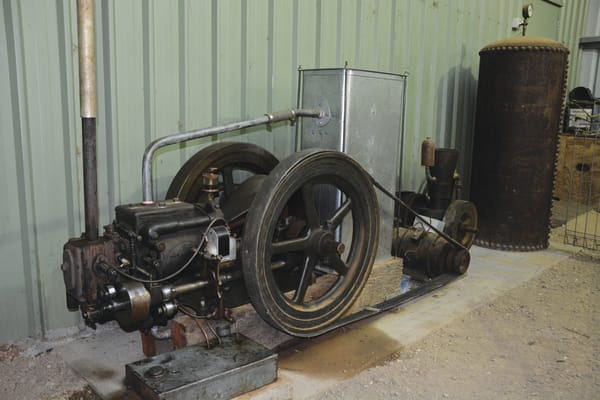
The Kelly & Lewis 3-throw displacement pump was attended to next. The valves were removed, freed up, and reseated. As the pistons were worn concave, a failure of the packing gland had occurred. With machining being required, resulting in a smaller diameter piston, the packing chambers had to be altered. A callout for scrap brass was made to club members, resulting in a bucket of brass taps to be melted down to form new packing gland rings. One inch square gland packing, 25ft in length, was sourced from the UK at a cost of $800 with all of it being used, leaving nothing to spare. The crankshaft was refitted, the plumbing was assembled to allow a water recirculation system, and an original fuel tank was utilised as a holding tank
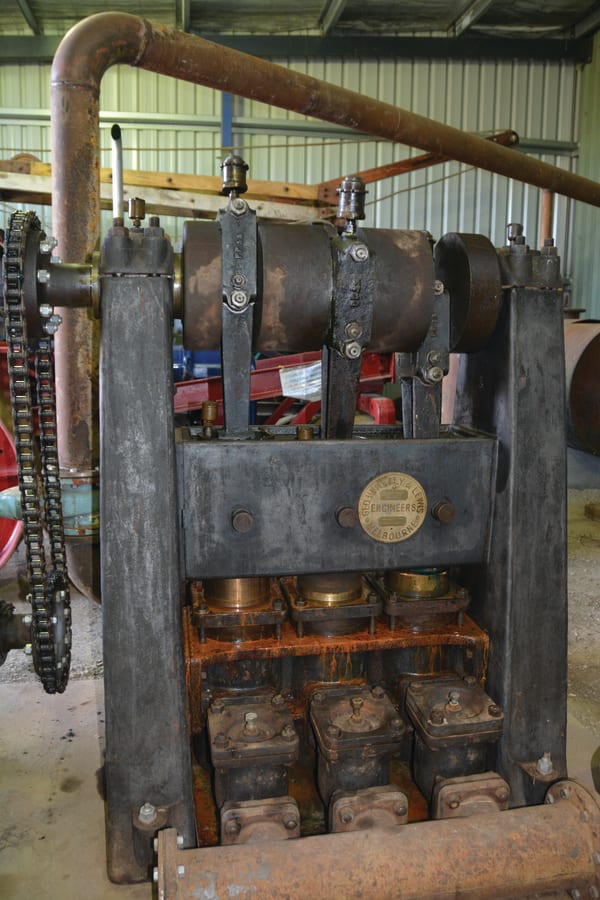
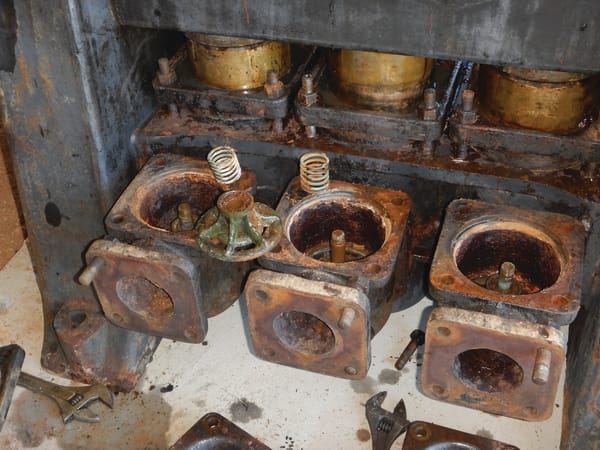
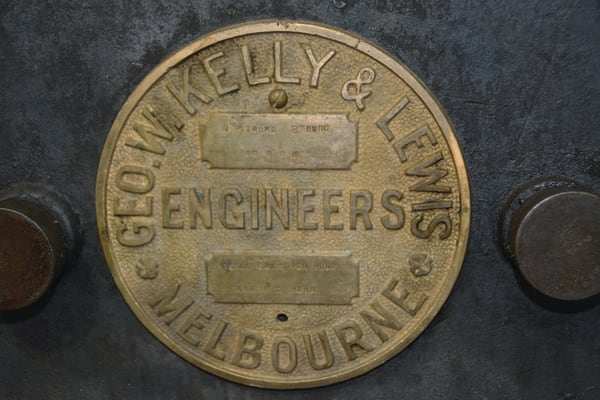
*Baw Baw Old Engine and Auto Club.
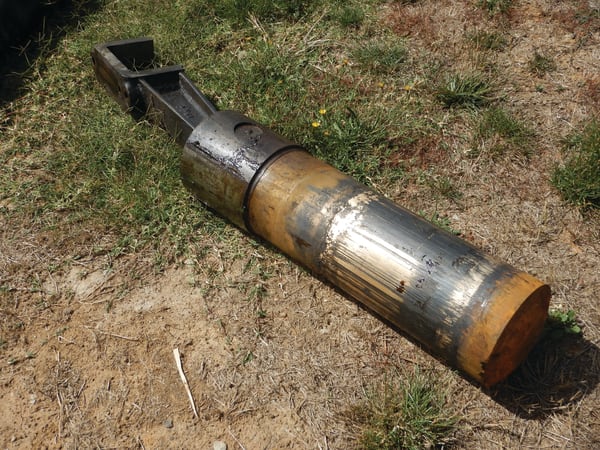
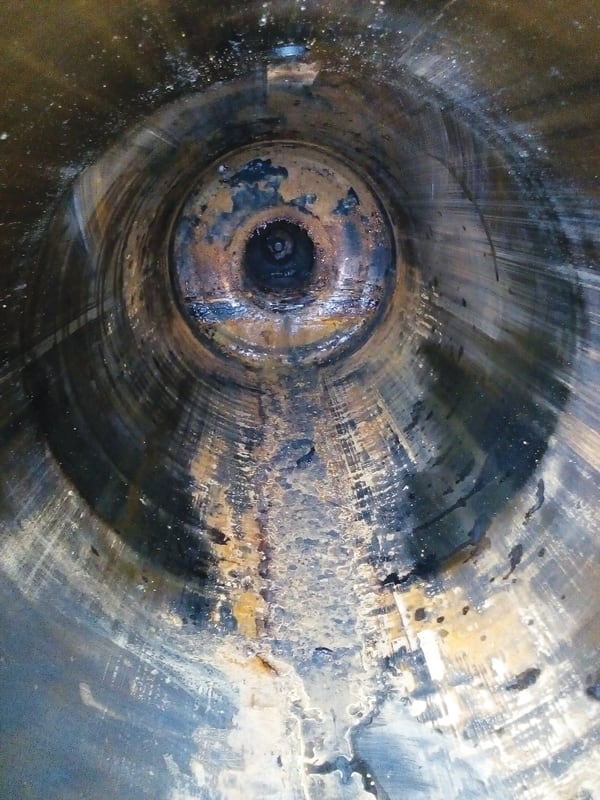
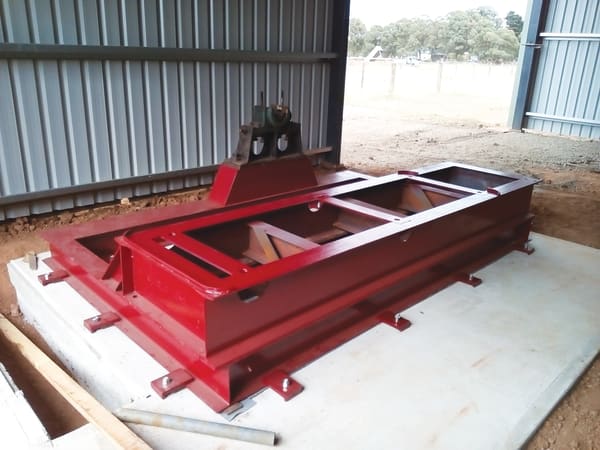
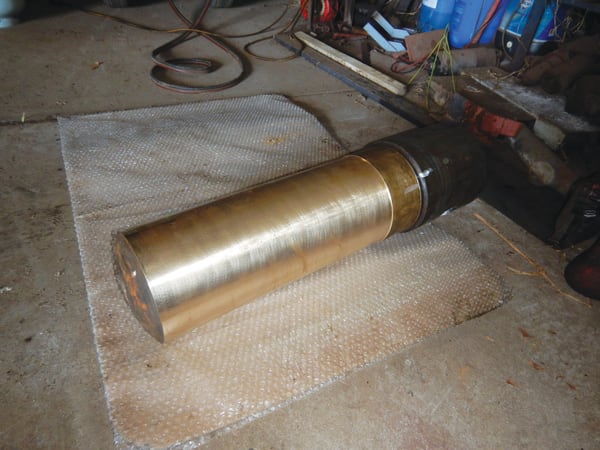
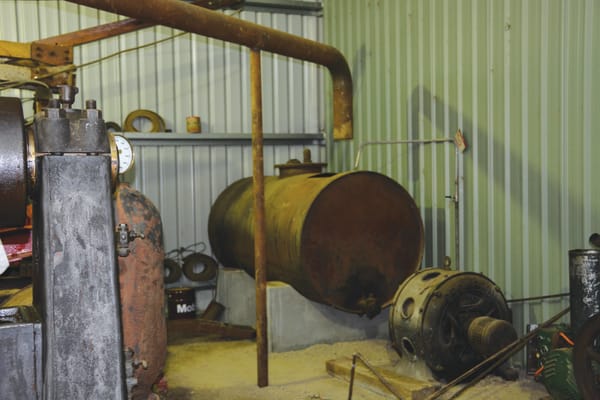
TIMELINE 1906-2019
26 July 1906:
Consulting engineer, Mr Thomas Fowler was engaged to establish the feasibility of a pump station at Rokeby.
1910:
2 x Hornsby & Sons 37hp gas suction engines were installed, driving Robison Bros 5-chamber centrifugal pumps.
February 1910:
Commenced operation.
April 1922:
Major pump repairs carried out.
1923:
50hp Crompton DC motor and 3-throw pump installed and the No. 1 Hornsby and turbine pump was removed.
January 1923:
Proposed 5-throw pump – did not eventuate.
February 1923: Tender accepted – 3-throw pump - £1,309 ($106,000).
September 1923: No. 2 Hornsby engine still working.
July 1924:
No. 1 Hornsby engine and pump offered for tender.
June 1926:
Electric motor and pump and the No. 2 gas engine working.
January 1929: Contract for supply by Ronaldson & Tippett.
1929:
Ronaldson & Tippett residual oil engine and 3-throw pump installed with the No. 2 Hornsby and turbine pump removed.
December 1929:
Ronaldson & Tippett engine commenced operation.
1949/50:
Metropolitan Vickers 75hp installed.
1957:
Brook Motors 150hp installed.
1963:
Pump station ceased operation.
1988:
Machinery removed and stored.
2014:
Transported to
BBOEC.
2019:
Engine, gearbox and 3-throw pump restored back to running order.
Items on Hand
Original 1926 Austral starting engine No. 7806;
Single-cylinder vertical air compressor, believed to be a Ronaldson & Tippett, with the original riveted air receiver – 200psi;
1929 Ronaldson & Tippett residual oil engine No. 7256, of 68hp at 300rpm;
Richardson gearbox twin-speed;
Kelly & Lewis 3-throw pump, 15,000gal per hour at 55rpm;
Generator - 1.5kw, 230v, 1,780rpm;
Crompton - 50hp;
Metropolitan Vickers Electric Company, 75hp, 400v, direct coupled to Harland Spiroglide 5” 5-stage centrifugal pump, 25,000gph;
Brook Motors Limited 150hp, 415v, direct coupled to Thompsons 8”, 3-stage centrifugal pump, 60,000gph;
Plus associated pressure vessels/air chambers.
SPECIFICATIONS
Ronaldson & Tippett residual oil engine No. 7256, 1929.
Bore: 113/4”
Stroke: 20”
HP: 68 @ 300rpm
Flywheel: 7’9” diameter
Face: 12”
Pulley: 4’ diameter
Richardson Gears Ltd, Engineers Footscray, 2-speed gearbox, manufactured 5 April, 1920.
Kelly & Lewis, Melbourne,
Triple-throw Displacement Pump
Stroke: 9”
Bore: 8”
RPM: 55
GPH: 15,000